News Center
Let the solar energy and the world combine perfectly
Aluminum frame experts say "steel" - analyze the defects of steel frame from the perspective of carbon emission, reliability, cost, etc.
Time:
2024-06-27
Introduction
Aluminum alloy frame has always been one of the most important auxiliary materials for photovoltaic modules. Although there have been frameless double-glass module products in photovoltaics, power station application problems occur frequently, resulting in a lot of loss and waste. Time has proved that aluminum alloy frame is one of the indispensable auxiliary materials for photovoltaic modules. With the demand for cost reduction in the photovoltaic industry, some manufacturers consider using steel frames instead of aluminum alloy frames. This paper compares the characteristics of aluminum alloy frames and steel frames, and the results analysis points out the shortcomings of steel in the application of photovoltaic frames.
I. Comparison of frame usage of photovoltaic modules
The density of steel is 7.85*103kg/m³, while the density of aluminum alloy is only 2.7*103kg/m³, the density of steel is 2.9 times that of aluminum alloy. Combined with the actual consumption of module products, consider 1GW photovoltaic modules, and calculate the actual consumption of aluminum alloy frame and steel frame. Considering that the strength of the steel frame is slightly stronger than that of the aluminum alloy frame, a similar frame structure is adopted. The wall thickness of the aluminum alloy frame is calculated as 1.4mm, and the wall thickness of the steel frame is considered to be 1.2mm and 0.6mm for practical applications.
Table 1: 1GW module steel frame and aluminum frame consumption comparison
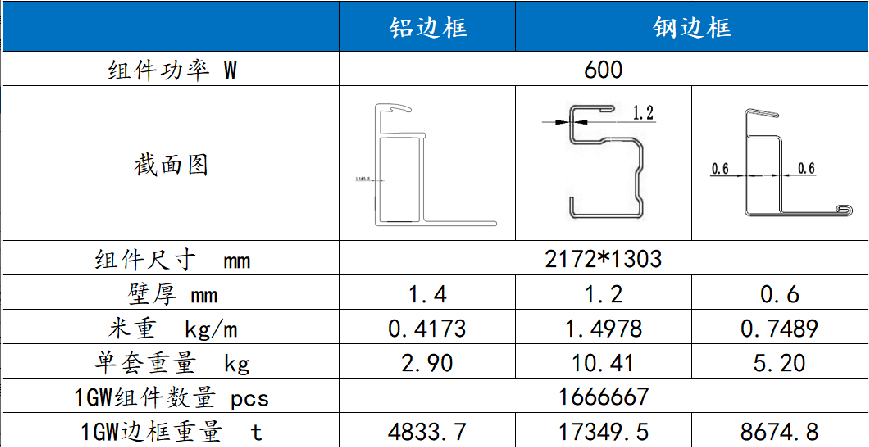
Comparison found that even if the steel frame adopts 0.6mm wall thickness, the weight of the 1GW module steel frame is 1.8 times that of the aluminum alloy frame; while the weight of the 1.2mm wall thickness steel frame will reach 3.6 times that of the aluminum alloy frame! Consider the steel frame The strength is relatively high. In this paper, the wall thickness of the aluminum alloy frame is 1.4mm and the wall thickness of the steel frame is 0.6mm for analysis.
II. Carbon emission analysis of aluminum alloy frame and steel frame in the whole life cycle
Under the "dual carbon" goal, the analysis of product energy consumption and carbon emissions should not only focus on the immediate, but should be analyzed from the perspective of the whole life cycle. The whole life cycle assessment is a process of evaluating the environmental load related to the whole life cycle of a product, process or activity from raw material collection, to product production, transportation, sale, use, recycling, operation and maintenance, and final disposal. A LCA begins by identifying and quantifying the consumption and emissions of energy and substances throughout the life cycle stages, then assessing the environmental impacts of these consumption and emissions, and finally identifying opportunities to reduce these impacts. The whole life cycle stage division includes: material and energy cycle in the whole process of raw material extraction, transportation, product manufacturing, product use, and product disposal. Here, we use the full life cycle assessment method to evaluate the energy consumption and carbon emissions of the aluminum alloy frame and the steel frame.
Table 2: Calculation of carbon emission factors in the whole life cycle
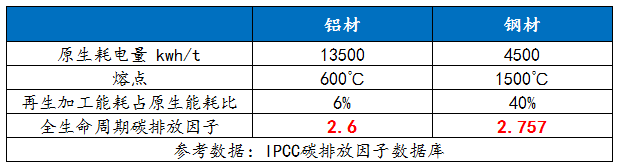
Although the initial power consumption of aluminum production is relatively large, due to the high melting point of steel, the recycling process consumes a lot of energy. Therefore, according to the evaluation of the whole life cycle method, the carbon emission factor of aluminum material in the whole life cycle has a higher carbon emission factor. big advantage. The carbon emission of the aluminum alloy frame of the 1GW module is 12567.6t, while the carbon emission of the steel frame reaches 23916.4t, which is about twice that of the aluminum alloy frame.
Due to the high recycling rate of aluminum materials, it basically reaches the level of more than 95%, and the price preservation rate of scrap aluminum after 25-30 years is high. It is estimated that the recycling value ratio of aluminum alloy frame in the whole life cycle is as high as 89.3%, while the recycling value ratio of steel frame is only 22.38%. For 1GW modules, the initial investment of aluminum alloy frame is 90.632 million yuan, the recovery value is 80.934 million yuan, and the sunk cost is only 9.698 million yuan; while the steel frame has an initial investment of 76.338 million yuan, the recovery value is 17.085 million yuan, and the sunk cost reaches 59.253 million yuan. For end users, the value-preserving properties of the aluminum alloy frame are obvious.
Three, product performance comparison
1. Thermal expansion coefficient and elastic modulus analysis
Photovoltaic modules were originally used with aluminum alloy frames. After decades of power station verification, their performance is compatible with glass and other auxiliary materials, and thermal expansion has never affected the power station. .
The influence of deformation caused by elastic modulus is far greater than that caused by thermal expansion. We analyze the elastic modulus of different materials and their matching. The specific data are shown in Table 3.
Table 3: Comparison of elastic moduli of different materials
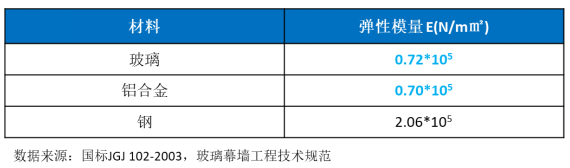
It can be seen from the data that the elastic modulus of the steel frame is much larger than that of the aluminum alloy frame and glass. In the context of large-sized components, the glass deformation is larger under wind or snow load conditions, and the aluminum alloy and glass keep synchronous deformation , can better protect the glass, which can greatly reduce the problem of explosion board in power station applications. Due to the large difference between the elastic modulus of the frame and the glass, and the low machining accuracy of the steel frame, it is easy to generate local stress concentration under the wind load or snow load, causing the module to explode.
2. Grounding Analysis
The surface of the conventional aluminum alloy frame is a non-conductive oxide layer, which has good insulation and withstand voltage performance. At the same time, in order to ensure grounding safety, specially reserved grounding holes. The currently used steel frame is galvanized aluminum-magnesium steel frame. The zinc-aluminum-magnesium coating has excellent self-healing ability. Salts Zn5(OH)8Cl2·H2O, Zn4(OH)6SO4·nH2O, Zn5(OH)8(CO3)2·H2O and Zn6Al2(OH)16CO3·4H2O, etc.), the corrosion products have a dense and continuous structure and poor conductivity. The increase of such corrosion products forms a dense protective film on the surface of zinc, aluminum and magnesium, which affects the grounding conductivity of the components, and poses a great safety hazard. That is to say, there are the following contradictions: the excellent self-healing ability of the steel frame at the grounding hole will affect its grounding performance and cause great potential safety hazards; The grounding hole is corroded and rusted until it affects the performance of the entire assembly.
3. Product weight impact analysis
The most intuitive change between the steel frame and the aluminum alloy frame is the change in the weight of the components. At present, with the increase of the size of the modules, the weight of the modules is more and more concerned by the power station practitioners. The main influences of the changes in the weight of the modules are as follows:
1) Impact on component transportation
When transporting goods, consider the weight and volume. Increased component weight will lead to increased transportation costs and transportation carbon emissions. Through calculation, the carbon emission caused by the transportation process is obtained, and the steel frame is more than twice that of the aluminum alloy frame.
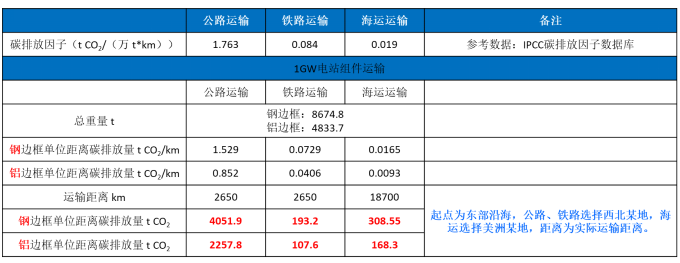
Table 4: Comparison of carbon emissions from 1GW module transportation at the same distance
2) Impact on application scenarios
The steel frame assembly per unit area is 1.5-2.5kg heavier than the aluminum alloy frame assembly. In addition, the weight of the aluminum alloy frame per unit area is about 1.5kg, and the weight of the steel frame is about 3.5kg. After installing the bracket, the steel frame assembly exceeds the load-bearing capacity of the conventional color steel tile roof by 15kg/㎡. The increase in the weight of steel-framed photovoltaic modules increases the risk of load-bearing under wind pressure and snow load, which limits the application scenarios of distributed photovoltaics. Similarly, in the current installation of rooftop distributed photovoltaic power stations, the color steel tile roof photovoltaic support has been changed from the original steel support to the aluminum alloy support, which is also to reduce the risk of load-bearing.
At the same time, the weight of the components increases, which makes the installation of the power station difficult, the installation cost increases, and there are also potential safety hazards.
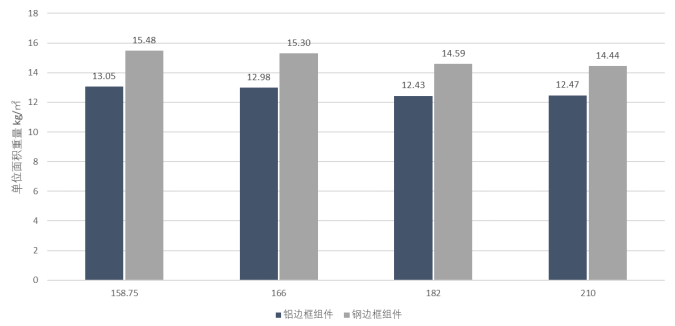
Figure 1: Weight comparison of steel frame components per unit area and aluminum alloy frame components
4. Other impact analysis
In the production stage of photovoltaic modules, the precision of the frame notch has a huge impact on the burst rate. The aluminum alloy frame is extruded through a die, which has high precision control, and the precision can be less than 0.1mm, and the rate of explosion in the component manufacturing process is extremely low. The steel frame adopts the cold-rolled bending process, and the production accuracy is difficult to control. Generally, the accuracy of the cold-rolled and bending equipment is ≤0.5mm, and the processing accuracy is likely to increase the production rate of the steel frame assembly. Similarly, on the application side of the power station, the accuracy of the notch leads to the concentration of stress points of the steel frame components under the conditions of wind pressure and snow load, and the result is prone to the phenomenon of component explosion.
In addition, the environmental conditions in the actual operation of the power station are much harsher than those in the laboratory, and many factors need to be considered and verified, such as the compatibility between silica gel and steel frame coatings or zinc-aluminum-magnesium coatings, the northwest, coastal and other places. Strong wind sand and seawater erosion performance, etc., all need to be verified by the actual measurement of the power station.
Four, company introduction
YONZ Technology was founded in 2009 and has been deeply involved in the photovoltaic industry for many years. It is the largest aluminum alloy frame supplier in the industry specializing in photovoltaic structural solutions, and also the largest frame supplier in the photovoltaic industry. Australia, Canadian Solar and other well-known customers. Leading corporate customers in the photovoltaic industry. There are three production bases in Changzhou, Jiangsu, Chuzhou, Anhui, and Yingkou, Liaoning, with an annual output of 300,000 tons of aluminum alloy profiles and a frame capacity of 40GW, ranking first in the world.
On November 17, 2021, the YONZ low-carbon recycled aluminum new material photovoltaic frame project with a total investment of 5 billion yuan was launched in Fanchang District, Wuhu. The project plans to have a total investment of 5 billion yuan. equipment, and build a photovoltaic frame production line with an annual output of 360,000 tons of low-carbon recycled aluminum new materials. After the project is completed and put into production, the group will form a 100GW photovoltaic frame production capacity, with an annual sales revenue of over 20 billion yuan, which will not only consolidate the group's leading position in the photovoltaic industry, but will also rank first in the aluminum processing industry.
Related News
YONZ Stock Listing Souvenir Creation Concept
2024-06-27
Contact Us
Address: No. 99, Yuehu Lake Road, Jintan District, Changzhou City, Jiangsu Province
E-mail:yzgf@yonz.com
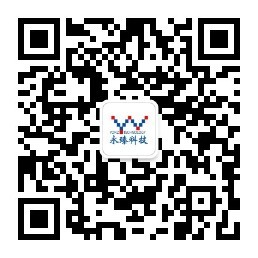
Pay Attention
© 2021 Yonz Technology Co., Ltd. Powered by: www.300.cn Changzhou