News Center
Let the solar energy and the world combine perfectly
Whether it is carbon emission, reliability, cost, aluminum alloy frame is the best choice ——Comparative analysis of aluminum alloy frame and steel frame
Time:
2024-06-27
Summary
Aluminum alloys are mainly used in solar photovoltaic frames and solar photovoltaic brackets in the photovoltaic field. Solar photovoltaic frames and brackets mainly play the role of fixing and sealing solar cell modules, enhancing module strength, and facilitating transportation and installation. Their performance will affect the life of solar cell modules. Of course, in the photovoltaic frame, there are also several other photovoltaic frames, such as: steel frame, polymer material frame and glass fiber reinforced plastic frame, etc. However, due to the light weight, strong corrosion resistance, easy forming, high strength, easy cutting and It has the characteristics of processing and recyclability, and is currently the most common application in solar frame.
Based on the concept of "the right material is used in the right scene", this article analyzes the difference between aluminum alloy frame and steel frame from the perspectives of energy consumption, recyclability, appearance, performance, reliability, economic value and other aspects of the whole life cycle. Features. The results show that aluminum alloy stands out as a structural material due to its own characteristics and has absolute advantages. The use of aluminum alloy frame for photovoltaic modules is the only correct choice for the development of the photovoltaic industry.
01 Introduction
The domestic photovoltaic industry started late but showed a momentum of rapid development. In 2002, my country's photovoltaic industry began to take off. During the "Tenth Five-Year" period, my country has successively passed the "National High-Tech Research and Development Plan" and "Technology Research and Development" plans in the research and development of photovoltaic power generation technology, shortening the gap between the photovoltaic power generation manufacturing industry and the international level. . In recent years, photovoltaic technology has been iteratively updated, and product development has been ups and downs. Through the continuous efforts of photovoltaic people, China's photovoltaics have become world-class. On October 24, 2020, the "Opinions of the Central Committee of the Communist Party of China and the State Council on Completely, Accurately and Comprehensively Implementing the New Development Concept and Doing a Good Job in Carbon Peaking and Carbon Neutralization" was released. The opinions clearly achieve the goal of carbon peaking and carbon neutrality, and mention that by 2030, the proportion of non-fossil energy consumption will reach about 25%, and the total installed capacity of wind power and solar power will reach more than 1.2 billion kilowatts. As the main force of the dual-carbon goal, photovoltaics should start from themselves and contribute to the dual-carbon goal.
In the course of photovoltaic development, improving module efficiency and reducing module cost have always been the two goals of photovoltaic people. Through years of research, the efficiency of photovoltaic cells has been continuously improved. At the same time, major mainstream manufacturers have reduced the cost of the module side through the optimization of different process combinations and auxiliary material solutions.
Photovoltaic aluminum alloy frame has always been one of the most important auxiliary materials for photovoltaic modules. Although photovoltaic has experienced the era of frameless double-glass modules, due to frequent problems at the application end of power plants, a large number of customer complaints and compensation have been caused. Time has proved that aluminum alloy frames are one of the indispensable auxiliary materials for photovoltaic modules.
02 Aluminum Alloy Frame and Steel Frame Whole Life Cycle Carbon Emission Analysis
As we all know, in the whole life cycle, the processing technology of aluminum is only electrolytic aluminum as a high energy consumption link, but considering the recycling characteristics of aluminum, the energy consumption and carbon emissions of recycled aluminum are only 3% of that of primary aluminum~ 8%, far less than the recycled steel processing link. Figures 1 and 2 are diagrams of the processing links in the whole life cycle of aluminum and steel, respectively.
Recycled aluminum only needs to melt scrap aluminum to remove impurities and add alloying elements, so the carbon emission is much lower than that of primary aluminum, but the electric furnace, rolling and other processes during steel recycling have a large amount of power consumption and carbon emissions.
With the vigorous development of the photovoltaic industry, the increase in installed capacity year by year and the expiration of the life of old modules, the number of decommissioned photovoltaic modules and their waste has gradually increased. As the world's leading photovoltaic country, China's photovoltaic waste problem has become increasingly apparent. The report of the International Renewable Energy Agency and the International Energy Agency's photovoltaic system project also proposes that by 2050, the total cumulative installed photovoltaic capacity in the world will reach 4.5TW, and only the retired components in the Chinese market can reach 20Mt (megatons). In the context of the upcoming wave of component recycling, we should not be short-sighted and only focus on current costs and investments. As the main force of the dual carbon goal, we should evaluate its carbon emissions from the full life cycle.
1) Analysis of the recovery rate of aluminum alloy frame and steel frame
Due to the corrosion-resistant properties of aluminum alloys, it is close to infinite recycling, with very little consumption. According to the International Aluminium Institute, 75% of the 1.5 billion tonnes of aluminium ever produced globally is still in use. The recycling rate of scrap aluminum in my country is higher than the global average.
Because of its corrosiveness, the recovery rate of steel has been maintained at the level of 55-65%, which cannot be effectively improved. Table 2 shows the recovery rate of steel.
2) Analysis of recycling energy consumption of aluminum alloy frame and steel frame
In the context of "double carbon", aluminum alloy also has lower recycling energy consumption and recycling carbon emissions during the recycling process. Compared with recycled steel, the carbon emission of recycled aluminum is 0.23t, which is only 22.3% of recycled steel.
3) Calculation of carbon emission factors for the whole life cycle of aluminum alloy frame and steel frame
In order to more accurately evaluate the carbon emission reduction capabilities of aluminum alloy frames and steel frames, the carbon emission factors of aluminum alloy and steel frames throughout the life cycle were calculated by searching a large number of documents. The calculation results found that the aluminum alloy frame has a lower carbon emission factor. In order to more intuitively show its carbon emission impact, taking a 1GW module as an example, the carbon emission data of the aluminum frame and the steel frame of the power station are converted, and it is found that the carbon emission factor of the aluminum alloy frame is only 52.35% of that of the steel frame in the whole life cycle, and the carbon emission is higher. Low.
4) Other carbon emission factors
The density of the steel frame is higher, the components are heavier, and the carbon emissions during transportation, handling, and installation increase accordingly. Here, we take the calculation of transportation carbon emissions as an example.
Only the carbon emission caused by the transportation process, the steel frame is twice as much as the aluminum alloy frame. Therefore, under the premise of the double carbon background, the aluminum alloy frame has better emission reduction effect, and can be recycled many times in the whole life cycle. The application of steel frame increases carbon emissions throughout the life cycle, which is not conducive to the green development of the photovoltaic industry.
03 Steel frame reliability and hidden danger analysis
Analyze the reliability and potential problems of the steel frame from the technical side. There are many hidden dangers such as machining accuracy, grounding, material matching, load-bearing, and appearance. The specific analysis is as follows.
1) Frame machining accuracy
Because the aluminum alloy frame is extruded through a die, it has high precision control. The precision of the conventional photovoltaic aluminum frame can be less than 0.1mm, while the steel frame adopts the cold rolling bending process, and the production accuracy of this process is difficult to control. , Generally, the accuracy of cold-rolling and bending equipment is ± 0.5mm. To improve the accuracy of cold-rolling equipment, a lot of investment in bending equipment is required. Because the accuracy is difficult to control, the following problems are prone to occur:
① The photovoltaic frame has high requirements on the accuracy of the notch, and the precision problem caused by the cold-rolling and bending process is particularly prominent at the notch, especially when the module is exposed to wind and snow outdoors, under the conditions of wind pressure and snow load , resulting in the concentration of stress points, and it is very prone to problems such as plate explosion. For example, some time ago, the explosion problem of a power station using steel frame components emerged one after another, and the accuracy was difficult to control is one of the reasons;
② Due to the precision defect of the steel frame, gaps are prone to appear at the connection of the frame, which first affects the appearance yield of the product. Secondly, when it is applied in the power station, water vapor is prone to infiltration, and coupled with condensation, the water droplets are on the steel frame. Internal condensation can easily lead to problems such as corrosion of the steel frame from the inside.
2) Hazardous grounding performance of steel frame
The surface of the conventional aluminum alloy frame is a layer of non-conductive oxide layer, which has good insulation and voltage resistance performance, but to ensure grounding safety, specially reserved grounding holes. The currently used steel frame is galvanized aluminum-magnesium frame, and the zinc-aluminum-magnesium coating has excellent self-healing ability.
However, due to its self-healing ability on the cut surface, the protective layer (type and composition of coating corrosion products, among which alkaline zinc salts Zn5(OH)8Cl2·H2O, Zn4(OH)6SO4·nH2O, Zn5(OH) 8(CO3)2·H2O and Zn6Al2(OH)16CO3·4H2O, etc.), the corrosion products have a dense and continuous structure and poor electrical conductivity. With the increase of such corrosion products, a dense protective film is formed on the surface of zinc, aluminum and magnesium (reference: "Research Status of High Corrosion Resistance Zinc Aluminum Magnesium Coating"), which affects the grounding conductivity of components. That is to say, there are the following contradictions in the application of steel frame: at the grounding hole, if it has excellent self-healing ability, it will affect its grounding performance and cause great safety hazards; The steel frame rusts from the grounding hole until it affects the performance of the entire component frame.
3) Material compatibility issues
Photovoltaic modules are a combination of various materials. As the veteran of photovoltaic modules, aluminum frame has passed the test of time and various harsh environments to verify that it has the best matching effect with photovoltaic modules. Although the steel-based magnesium-aluminum-zinc steel frame material has better mechanical properties than the 6005-T6 aluminum alloy material in terms of tensile strength and other mechanical properties, the photovoltaic module, as a combination of multiple materials, has a higher priority of material matching than a single material. material properties.
The elastic modulus of the aluminum alloy frame is close to that of the glass, and it has better synchronous deformation ability. The elastic modulus of the steel frame is too large, and the machining accuracy is low. When the wind pressure and snow load, it is easy to generate stress points, which will cause the components to explode.
Similarly, the material compatibility, that is, the combination of silicone and aluminum alloys, has also been time-proven, while the compatibility of the steel frame and the existing silicone has not been verified by the power station, and there is a greater safety hazard.
4) Weight bearing problems
The steel frame assembly per unit area is 2-2.5kg heavier than the aluminum alloy frame assembly. In addition, the weight of the aluminum alloy frame per unit area is about 1.5kg, and the weight of the steel frame is about 3.5kg. Considering that after installing the bracket, the steel frame assembly exceeds the load-bearing capacity of the conventional color steel tile roof by 15kg/㎡. At present, in the installation of rooftop distributed photovoltaic power station, the color steel tile roof photovoltaic support has been changed from the original steel support to the aluminum alloy support, which is also to reduce the risk of load-bearing. The increase in the weight of steel frame photovoltaic modules increases the risk of load-bearing under wind pressure and snow load, which limits the application scenarios of distributed photovoltaics.
5) Product Appearance
Appearance is a common problem. After extrusion molding, the aluminum alloy frame has an excellent metal appearance after sandblasting and oxidation. However, the steel frame is difficult to be accepted by the public due to its uneven appearance due to material characteristics. . I won't do too much analysis on this here.
In the northwest, seaside and other areas, strong wind and sand have a strong corrosive effect on the coating. After years of empirical evidence, the aluminum alloy frame has verified its performance in harsh environments. However, at present, the steel frame has not been rigorously tested for this experiment, resulting in hidden dangers in its application.
Analysis of recycling value of 04 aluminum alloy frame and steel frame
Considering the recycling value, the PV modules will be recycled after the expiration of 25-30 years, and the aluminum alloy frame modules have higher recycling value. It is estimated that the recycling value ratio of the aluminum alloy frame is as high as 89.3%, while the recycling value ratio of the steel frame is only 22.38%. Although the initial investment is slightly higher, the recycling value of aluminum alloy determines the economy of its value preservation and even appreciation.
05 Conclusion
Time is the best litmus test, and aluminum alloy as frame material has been accompanying the development of photovoltaic industry. Appropriate materials are used in suitable scenarios, and practice is the only criterion for testing the truth. Compared with steel frames, aluminum alloy frames have absolute advantages in terms of carbon emissions, recyclability, reliability, and value throughout the life cycle. The use of aluminum alloy frame for photovoltaic modules is the only correct choice for the development of the photovoltaic industry.
Related News
YONZ Stock Listing Souvenir Creation Concept
2024-06-27
Contact Us
Address: No. 99, Yuehu Lake Road, Jintan District, Changzhou City, Jiangsu Province
E-mail:yzgf@yonz.com
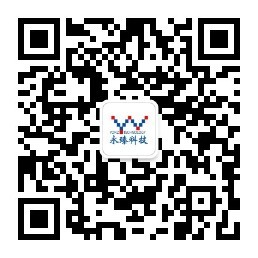
Pay Attention
© 2021 Yonz Technology Co., Ltd. Powered by: www.300.cn Changzhou